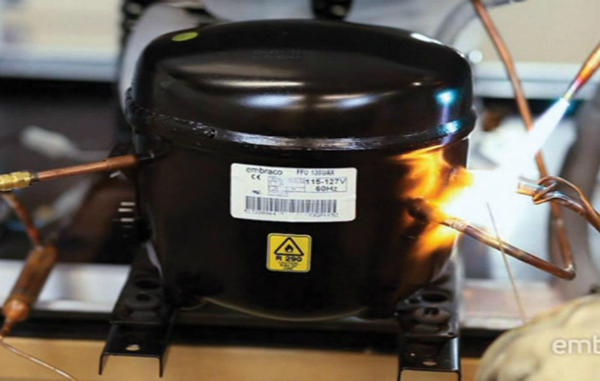
Knowledge of welding (or brazing) is essential for all refrigeration contractors. It’s important to use proper procedures while maintaining safety and ensuring the successful outcome of the operation. So in this edition we’ll show the best practices for welding and joining tubes without solder.
With Solder The conventional torch is not ideal for this type of work, using the two nozzle model mounted on a ring structure is recommended, which allows flame application on both sides of the tube. The advantages are higher quality and productivity, less torch movement, faster preheating or heating as well as higher solder penetration. Most refrigeration contractors use oxy-acetylene welding where the heat is generated by combining oxygen (comburent) and acetylene (fuel). Â
Welding – step by step
1-Â Â Â Start by cleaning the material to be welded, eliminating traces of oil, grease, rust or any other substance. If there is paint, remove it with the help of sandpaper.
2-Â Â Â Expand one of the tube ends and fit the other end inside it (about 10 mm).
3-Â Â Â Prepare the torch for use by installing pressure regulators on the oxygen and acetylene cylinders and check for leaks.
4-Â Â Â Fit the nozzle on the torch according to the material to be welded.
5-Â Â Â Light the torch and set it to the appropriate flame for the materials to be welded:
6- Choose the appropriate weld rod, and when the weld is not copper-copper also the appropriate flux (which serves to prevent oxide formation and facilitates the connection between the rod and the tube).
7- If applicable, spread the flux on the end of the expanded tube, using a stick or a brush.
8- Preheat the tube to be welded, keeping the flame about 2 cm away from it and making circular motions.
9- Put the flame on the tube’s expanded end and proceed according to each material type:
- Copper-copper: keep the flame on the tubes until they’re reddened, then touch the tip of the rod on the expanded junction and weld around the tube.
- Copper-steel or steel-steel: keep the flame until the flux becomes bright in color and then touch the rod on the expanded junction and weld around the tube. Pull back the flame when the solder flows around the tube.
10- Clean the weld location with a wire brush (copper-copper welds) or with a wet burlap cloth (other welds), make sure all is in order and, if necessary, redo. Without Solder It’s possible to join cooling system tubes without soldering them, using the Lokring System, developed by Vulkan. The process is quick, safe and efficient, requiring, in addition to Lokring connectors, only the use of an appropriate hand tool and the Lokprep seal.
This is a very good solution, which ensures complete sealing and is especially suitable for applications in which brazing is not recommended. It also allows joining tubes in locations such as the inside of plastic cabinets. The system is suitable for all metal tube types commonly used in cooling systems: steel, aluminum, copper and brass. The union can also be made between tubes of different materials such as aluminum-copper, aluminum-steel, etc. There are tube connectors for diameters ranging from 1.6 mm to 35.0 mm. See how simple it is to use the Lokring system, which requires just four steps: