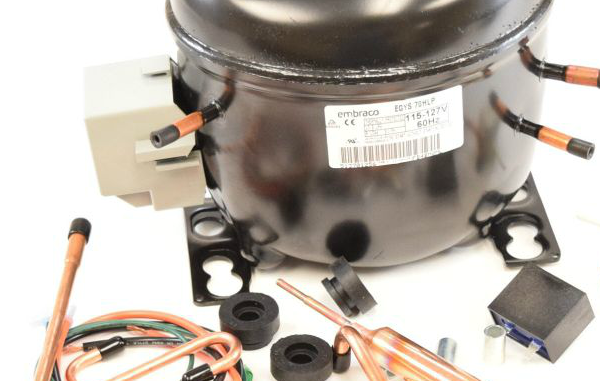
Know what to do in choosing and installing, to avoid this problem.
Embraco compressors are high-tech components, built to last many years. Rendering them useless is a big loss for the consumer and the technician and therefore mistakes leading to this should be avoided at all costs.
To ensure the best results, the correct posture to be adopted is to always follow the recommended procedures in two crucial moments:
- When choosing the compressor model to be used;
- At the time of its installation.
Some examples of the problems caused by not following these procedures can be seen in the photos below.
Incorrect choice of the compressor can cause several problems, among which the most serious is rendering it useless. It’s necessary to be attentive to the tips we gave in this section in the previous edition (Club No. 121, March / 2015), regarding the five main aspects that should be taken into account when choosing the most appropriate model:
1. Cooling capacity required by the system;
2. Evaporation temperature range (L/M/HBP);
3. Starting torque;
4. Voltage and frequency of the power grid;
5. Refrigerant fluid used.
To address the problem of rendering them useless, we address points 1, 2 and 3 which are listed above. We believe that the risks of wrong voltage and frequency are known to all.
In the case of refrigerants, the use of an incorrect choice of gas charge, low quality refrigerant, different refrigerant than that specified in the compressor label can cause numerous problems.
If the cooling capacity is not adequate, the compressor can perform very short on and off cycles, causing the compressor’s starting system to be overloaded. It may also stay on longer than it should.
In both cases, the durability of the electrical components and the mechanical compressor kit will be impaired due to higher wear than normal.
An important tip to check if the capacity is within the expected range is to observe the compressor’s duty cycle: it must stay on from 40% to 60% of the time. That is, the compressor should start from 4 to 6 times in an hour and remain on for 24 to 36 minutes during this period.
Regarding the motor’s starting torque (LST / HST), there will also be serious problems with the incorrect choice.
If a LST compressor, designed for use with capillary tube, is used in an application with expansion valve or un-equalized pressures, it will not start. The thermal protector will trip and this can lead to failures in electrical components.
The application range (L/M/HBP) is another essential characteristic to be observed, since each compressor design has its own characteristics.
If the compressor is not within the correct application envelope (that is, if it’s not used in a system operating with adequate condensing temperatures and evaporation), several issues may occur: from excessive heating of the compressor to a complete failure.
In addition to the items mentioned in the list above, another aspect to consider is the type of ventilation approved for the compressor model. This is a characteristic that needs to be observed, so as to not create risks to the component.
If a compressor designed for forced ventilation is used with static ventilation, it will overheat, causing a number of problems and leading to its failure.
If the incorrect use is the other way around, (using static rather than forced) the ventilation can “trick” the thermal protection system, allowing the passage of a high current and causing the compressor to burn out.
Improper installation
Several problems in the compressor, which may cause it to become useless or its burnout, stem from mistakes made at the time of installation.
In order to prevent them, it’s necessary to follow the procedures recommended by the manufacturer. They can be found, in detail, in the video about changing the compressor produced by Embraco and also in an article published in this section of the Club No. 113 (both are available on the Club’s website).
Briefly, the main process steps for installing a new compressor are:
- Clean the system;
- Replace the filter drier with a new one;
- Connect the discharge and suction tubes on the new compressor and weld the tube on the process passer;
- Check the welding points, to avoid tube clogging and leaks;
- Perform a proper system vacuum;
- Install electrical components in the correct sequence;
- Apply the gas charge using a scale and charge weight in grams as specified on the refrigerator;
- Seal the refrigerant circuit.
By correctly following the technical recommendations briefly summarized here, the risks to render the compressor useless by an error in its installation are eliminated.